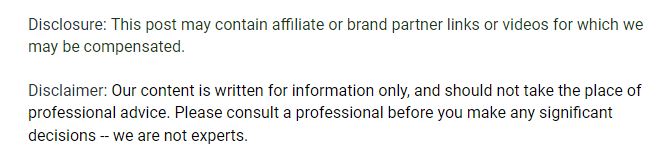
Insulation is very important in any building. Most of the time, you want to have some way of keeping the interior of the building separate from the exterior in terms of temperature. There are many days where it is simply too cold or too hot for the interior of the building to be the same temperature as the outside. This is why different types of insulation, such as spray foam, can be very important.

If you do not know a lot about spray foam or other types of insulation, it is possible that you have many questions. For example, you might wonder, what are the best insulation installation services in my area? If I do not have the money to hire a service, is there at-home spray foam insulation that I can use? What is the best canned spray foam insulation that is available? Where can I find the best-expanding foam filler? What is the best spray foam equipment that is available in my area? It would be a good idea for you to do some research on spray foam so that you can learn more about it. It would also be a good idea to talk to insulation professionals and see what they have to say on the topic.
Your spray foam rig is a valuable and powerful tool for insulating a space, sealing air leaks, and slashing monthly energy bills by as much as 20%. Like any tool, though, proper maintenance and cleaning of your spray foam parts and equipment are essential to keeping it running smoothly. If you maintain and clean your spray foam parts, you can minimize maintenance costs and be sure your spray foam insulation is always applied right.
Electricity and Air
Your spray foam insulation machine uses compressed air and electricity. Keeping all your spray foam parts working well starts with these two items. The air supply needs to generate both enough pressure and enough volume to drive the system so that no off-ratio material or blisters form. The air needs to be clean and dry because wet or dirty air can underpower the system and materials will not mix correctly. As for power, you should check it with an amp clamp meter. This should be done every day and is a simple way of making sure that you always have consistent power. Make sure the voltage you are using is consistent with the required voltage listed on the machine’s plate. Voltages that are too low can cause a machine to overheat and damage your spray foam parts. If you’re powering your spray foam equipment with a generator, make sure that the generator never runs out of fuel while the spray foam insulation machine is running to avoid damaging the circuit board.
Managing Screens and Monitors
The screens and strainers between your transfer pumps and your proportioning pumps keep anything you don’t want out of your material. Meanwhile, the inlet monitoring system reads the pressure and temperature of your materials as they transfer to the proportioning pumps. It’s important to always monitor the information provided by this system so sudden temperature and weather changes don’t cause you problems. The inlet monitoring system should always be kept clean and checked before operation. The filter should be inspected twice a week, or as needed, especially when new material is being put in or if the transfer pump pressure begins to fluctuate. Look for particles that are too large that may have been introduced to the pump, as these make keep the ball from properly seeding against the bevel, resulting in inaccurate pressure readings.
Monitor Your Transfer System
Your transfer system moves the material from its drums to the main proportioning pumps. Your transfer system will include a desiccant dryer. This is necessary because as the material level within the drums drops, air begins to displace the material. This air will have moisture in it, which the desiccant dryer removes from the system. This keeps crystals from forming and clogged the filter screen or building up over time in the transfer hoses and heated hoses. This is one of the main reasons for problems with your spray foam parts, and it can be avoided by making sure the desiccant dryer and its cartridge are inspected regularly. It’s also important to check on all the hoses and lines and clean them of any solid material whenever you change out a drum. If you notice the air hoses or transfer hoses have bulges or leaks, they should be replaced immediately. It’s important to look most carefully for leaks where the fitting is crimped to the hose.
Your Spray Foam Gun
Of all the spray foam parts, one of the most intricate is the spray gun. The spray gun mixes the two components under high pressure at just the right ratio and temperature. It’s important to check the air purge of your spray gun for condensation. Also check the filter screens every day and clean them as necessary or whenever the pressure of the material seems to be out of balance. Never allow the gun to get dirty.
Keeping your spray foam parts clean and in good order ensures your spray foam insulation equipment works properly for a long time to come. Be sure to replace spray foam parts whenever necessary to ensure the longest, trouble-free life for your machine.