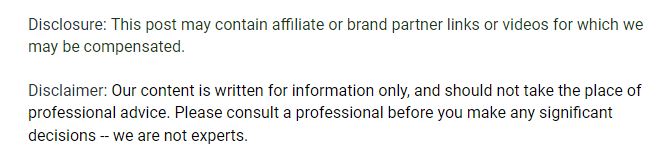
Barcodes are a vital component of warehouse operations. Barcode labels help manage inventory, initiate new orders, confirm employee identification, and automate countless other tasks. However, the many benefits of using barcodes can be undermined by a poorly performing printing and labeling operation if it results in difficulty scanning them. This is why barcode verifier and validator technology have become so critical: by verifying and validating barcodes, businesses can ensure they maintain print quality and data integrity.
- Barcode Verification: What is it and why do I need it?
Verification is the process of confirming print quality of a barcode using ISO and ANSI standards, and confirming the data content format meets application standards. The ANSI standard uses familiar letter grading, whereas the ISO/IEC standard provides numeric grades. Using a standards-based barcode verifier is a must. Even if regular scanners can read the code, other scanners further down the supply chain may not be able to. Verification ensures readability along the entire chain. - Barcode Validation: Matching the Right Data to the Right Product
Validation confirms that the correct barcode information applies to the correct product. This may also include checking the barcode size, position on the product, and potential elements that could interfere with scanning. Rather than needing a purpose-built barcode verifier, validating requires a fixed-mount scanner reads the codes on a production line, and a software solution then alerts the operator if there is a missing or incorrect label. While the results are more subjective in nature, it is critical to validate barcodes in order to prevent a number of costly operational failures. - Barcode Verification Vs. Barcode Validation:
While similar in nature, these processes yield quite different results, however both are equally important.Verification:
- Ensures print quality and scanability of the barcode
- Standards-based
- Requires a purpose-built barcode verifier
Validation:
- Evaluates the accuracy of the barcode data in relation to the product
- Subjective, based on company requirements
- Can be conducted using any scanning equipment
- Machine Vision Technology
Machine vision provides optical, non-contact sensing to extract information from digital images for process control or inspection. These systems use vision or 3D displacement sensors to evaluate products, confirming the proper size, measurement, shape, or configuration of products. In barcode verification or validation, these systems allow companies to automate the process of ensuring they print readable barcodes that:- Can be read with a scanner
- Are in the proper orientation
- Do not contain any defects
- Are the correct size
- Mission-Critical Quality Control
As barcodes are increasingly important to automating data collection and asset tracking, ensuring they can be consistently read and contain the correct data is crucial. There are a variety of barcode verifier and validator solutions and models available at a wide range of price points. Integration partners like Imprint Enterprises can provide expert guidance in finding the right solution for your business, as well as integrating verification and validation into your existing operations.