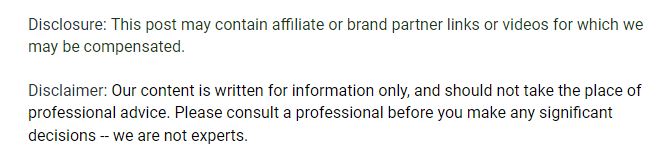

Load cells are important for sensing force, and the five types are dependent on the primary and secondary element that is used to sense the force. These are strain gauge type load cells, hydraulic load cells, diaphragm load cells, spool type load cells, and ring type load cells. These cells can operate under extreme conditions, such as very high or very low temperatures. There are many measurements engineers need to constantly know about these cells in order to confirm their accuracy, especially since machines are under extreme stresses. An important one is knowing torque measurements on rotating equipment. Since the torque force can change the ability of the machine to complete its job, having a torque sensor can validate the load cell accuracy.
Many machines use a more evolved form of a torque wrench to precisely apply a specific torque to as fastener such as a nut or bolt. This torque wrench was invented by Conrad Bahr in 1918 while working for the New York City Water Department. Torque measurements on rotating equipment use sensors similar to the one invented long ago by Conrad Bahr, and can work under extreme strains, although it does require some repair and maintenance. Calibration is necessary to keep the measurements in check, and to make sure they remain accurate. This involves comparing the measurements of two different instruments, one of which contains a known magnitude or correctness, simply called the standard device. This standard device can be used against the machine under testing to determine accuracy. Typically, recalibration needs to occur at least every two years, based on ISO9000 and other standards. The recalibration should be done more frequently if instrument deterioration is significant during that period, or more than 1%. Logically, recalibration more often simply leads to more accurate measurements more often, so it can never be done too much.
Sensor systems do work, and they work well. For example, an electrochemical fatigue crack sensor system can detect cracks in the field as small as 0.01 inches in an actual structure. This is similar for torque measurements on rotating equipment. The measurements are known to be highly accurate and important to machine functioning. Many weighing systems use load cells. This is because they offer non-intrusive, highly accurate load measurement data. This allows the machine to work the way it should work, without altering parts to enable the activity of the weighing system. Properly installed and calibrated load cells routinely achieve accuracies of around 0.03% to 1%, depending on the load cell type.
Load cells and their corresponding torque sensor units are designed to operate in a wide range of temperatures, from -452 degrees F all the way up to 450 degrees F. This means you can determine torque measurements on all types of rotating equipment, regardless of the region it’s located in, or the temperature it has to reach. This is beneficial because reactions have to occur at different temperatures to work efficiently. The machine does not have to be moved or altered in any way to get the torque measurements, because the sensors will work at the temperature suitable for that machine and process. This decreases the possibility for breakage of the machine or any of its parts, as well as the time it would take for an employee to retrieve the torque measurements. This would help cut costs because the manpower it takes are negligible, and the machine will run more accurately or be fixed in a more appropriate time frame if these measurements are taken.
Knowing torque measurements on rotating equipment is vital to machine processing and functioning. The measurements are highly accurate and proven to be accurate repeatedly. For example, most load cells use strain gauge technology, which is very well established and has been proven for more than 40 years. The sensors must be calibrated, though these calibrations generally last for years, and result in fewer machine breakdowns and repairs. The sensors can work in a variety of extreme conditions and stresses, so machines do not have to altered to retrieve the measurements, which saves time and money. Most importantly, knowing these torque measurements allows for confidence in your machine and its proper functioning.