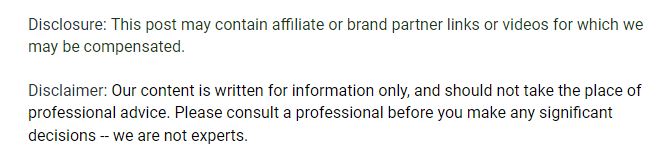

When planning the prototype PCB assembly for your project, it is important to keep an eye out for two crucial steps you will need to address at the end: the design for manufacturing and the panelization. We know that the final printed circuit boards will be routing signals and powering the electrical components, but it is worth noting that if the finished prototype has features that don’t translate well to the panelization stage your engineers will need to make some tweaks. While a the purpose of a prototype is to test the idea, there’s no reason you should make more work for yourself by not keeping the endgame in mind either, in this case manufacturing and shipping.
Can DFM and Panelization Help Create a Streamlined Prototype PCB Assembly?
Let’s quickly review PCB design:
So the primary insulating epoxy, FR4, is laminated with a thin layer of copper on either one or both sides, followed by the etching of circuitry interconnections to create a rigid prototype printed circuit board.
If it is a particularly complicated PCB, the complex layers will be added in layers.
The silk screen printing, liquid photo imaging, and ink jet printing are the three methods used to print the legend. The legend contains the component designators, switch settings, test points, and other indicators necessary for assembling, testing and servicing the PCB.
PCB design and layout determines later panelization. As OMNI Circuit Boards states, panelization is meant to “secure PCB boards during manufacturing, shipping, and assembly process.” We don’t want the boards to be damaged in transit.
Remember That This Prototype Will Eventually Need to Be Put in a Box For Shipping.
During the prototype PCB assembly stage it is helpful to remember that the electronic design of the board, meaning the component clearance, will determine its panelization. The PCB construction, the thickness of the board, all these little factors will have consequences later on even after the prototype is finished and operating as it should. Which brings us to what the design will be for manufacturing.
DFM asks, “How can the actual model of this PCB be safely shipped?” The prototype PCB assembly must consider if certain features will cause trouble during transit. Manufacturing, and the eventual shipment in terms of the supply chain will determine if the final product is met with success. If the PCB is damaged during shipment because of its design features, it has failed.
Engineers of printed circuit boards must consider their creation from its earliest stages to its final destination. Keeping the processes of DFM and panelization technology in mind as they design the prototype can lead to a more streamlined process, with less trips back to the drawing board.