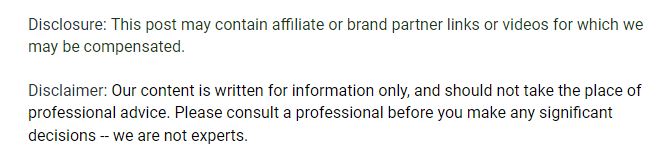
What’s the difference between a functional office space and an area that only promotes distraction and lost dollars? Believe it or not…it’s portability.
Times are changing. More workers are needing flexible schedules, remote jobs are rising higher than ever and eco-friendly designs are becoming the new standard. The warehouse office (also known as the modular office or the portable office space) is a smart way of achieving a little bit of everything in one happy package. Employees will have a comfortable space to work and study in, employers will save money on costly building materials…even the environment will enjoy a break from routine. To put things plainly, everyone benefits from the warehouse office in one form or another.
Learn your way around the modular office below and become familiar with all the ways you and your workers can save money.
How’s the construction industry looking, anyway? Back in 2011 prefab and modular construction was seen as a particularly popular time for the warehouse office in commercial applications. An extensive survey revealed a solid half of respondents using these processes for healthcare facilities, with another 40% using them for dormitories and general college buildings. Look around your city next time you’re making a run to the grocery store. You might just spot a few modular offices or prefabricated office spaces cropping up in your neighborhood.
A major reason why modular buildings are becoming so popular is their cost-effective model. They just streamline a very old process and make it more approachable for businesses of all shapes and sizes. The two types of modular construction available today are permanent and relocatable. Anywhere from 60% to 90% of all prefabricated construction occurs in either a warehouse or factory, though projects are generally completed much faster no matter the final result. Modular methods allow for speedy construction times while still maintaining quality.
How does this work, exactly? Modular constructions reduce energy consumption during the building process by an estimated 65%, later reducing energy costs for the occupants. It also does away with common building materials to craft a more fine-tuned end result. According to a study by UK-based WRAP (or Waste And Resources Action Programme), modular construction reduces wasteful materials by 90%. That’s cement, timber, wood pallets, shrink wrap, cardboard and cement, among others! As you can imagine, that saves countless industries a lot of money and reduces strain on the environment.
Hotels are especially loving the benefits of the in-plant modular office style. One report found the Marriott International pledging to modularly construct nearly 15% of its North American developments in 2017. This has extended to plenty of other industries, of course, and it’s widely considered by most construction professionals today the warehouse office will become the new standard. Your business stands to benefit mightily from the combination of less waste and faster production time, letting you and your workers get to work sooner.
Warehouse offices are timely, eco-friendly and incredibly easy to build. Around 90% of engineers, 85% of contractors and 75% of architects today either predominantly or partially use prefab construction processes on their projects. A report provided by the Building Industry Association Of Philadelphia estimates going modular can reduce construction costs between 10% and 20%. You can also cultivate more flexible workers by providing them multiple places to set up shop and strut their stuff. At the risk of sounding redundant?
Everyone wins. Look into the warehouse partitioning system next time your business expands and watch your savings skyrocket.