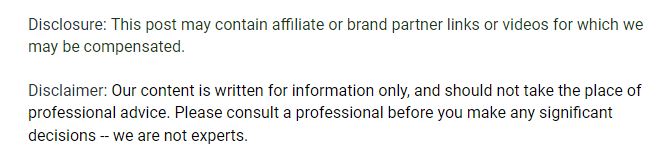
The United States and many other industrialized nations around the world make use of heavy machinery in factories and large vehicles to carry out all kinds of work, from digging to mining to construction and more, and these mammoth machines will sometimes suffer mechanical issues. No one wants a dump truck or a gas turbine to break down and become unsuitable, but inspecting these machines correctly can be difficult to do with the naked eye, and replacing and fixing parts deep inside a machine may be difficult as well. Naturally, some devices have been invented to deal with these issues, such as those used by borescope inspection services. Just what is a borescope? Borescope inspection is done with a device that has a long, flexible cable that can be inserted deep into a machine, and a camera and other sensors at the tip will transmit data to the handheld part of the device, and readings or a video feed can provide useful information to anyone carrying out the borescope inspection. Some factories or construction crews might be able to carry out borescope inspection themselves for turbine support or parts removal, but sometimes, borescope inspection is a labor that can be hired from the outside. What kind of machines will need a borescope inspection, and how often?
The Machines
Some of the technology used by industrial nations such as the United States are decades over over a century old, but they are time-proven ways to get work done, such as a turbine. These machines use rotating motion to generate power, such as power plants or, in years past, in steam-powered vehicles, anything from a tugboat to the famous Titanic and its sister ships. Coal-powered turbines start by coal being shoveled into a furnace that burns them, and this heat will boil water whose steam will travel through narrow tubes with great pressure. This pressurized steam then strikes turbine blades and cause the entire assembly to rotate, creating power. Such turbines in the past were used to propel ship propellers or train engines, and today, such turbine are more often used in traditional power plants.
Steam turbines were a staple in decades past, but today, most workers favor Combined Cycle Gas Turbine (CCGT) technology. A plant using this turbine type can achieve thermal efficiency of about 62% base-load operation, and this compares favorably to steam-powered plants, whose efficiency is limited to the 35-42% range. Gas turbines can also operate at a much higher temperature than steam types, where gas turbines operated at 2,000 degrees Fahrenheit and steam operates at a max temperature of 1,200 degrees Fahrenheit. And some turbines out there are part of the “go green” initiative, most famously wind farms. A wind turbine uses natural wind power to rotate the blades, and this motion generates electricity that can be sent all over a power grid. The advantage of wind turbines is that they generate no by-products of any kind, and are often used as non-polluting alternatives to fossil fuel power plants. Wind farms can be found across the world, and can even be installed in shallow water where they don’t take up room on dry land.
Turbines, engines, and more will sometimes corrode, break down, or get something stuck in them, and this calls for inspection with the right tools such as a borescope inspection job. If a power plant is suffering issues with its turbines, the managers can call for a borescope inspection crew to visit and use these flexible tubes to explore deep in a turbine assembly to find a problem with camera feeds or other data like temperature readings. It may dangerous or even impossible for an actual person to reach the area where a turbine is having problems, which is where a borescope is used instead. Other devices like tanks of dangerous liquids or vehicle engines can also be inspected in this manner, or even natural formations like caves or other natural features may be explored, such as at a mine or a future construction site. An inspector crew can purchase whatever borescope models they believe they need, for a variety of jobs such as visual data, reading temperature or air pressure, or any other metric that a business client would need measured on the job.