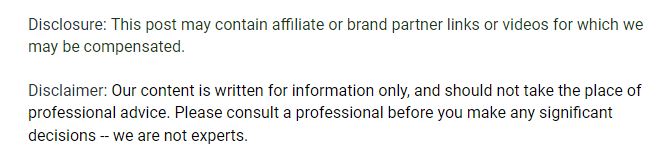
The quality of your equipment matters.
It’s why your clients and customers choose you over the competition. It’s how you save money in the long term. Quality begets quality, as the saying goes, and there’s a lot to gain from using the right materials from the get-go. Custom bellows are one of today’s most hidden and most utilized resources, responsible for powering our cars and keeping our plants running smoothly. Should you be doubting the quality of your bellows, the only logical step is to consider the missing pieces and adjust accordingly.
From the materials to the construction process, every step should be considered carefully.
How familiar are you with your metal properties? Even if you have years of experience under your belt, it never hurts to refresh yourself with the basics. Every type of metal has its own unique melting point, essential for bringing out the best in your bellows. Iron ore, for starters, generally melts at 2,750 degrees Farenheit. Compare this to steel, which has a melting point of 2,500 degrees Fahrenheit. How pure your metal is will have an effect on its durability, longevity, and reaction with certain materials.
One material you should be familiar with is the ‘Hastelloy X’ alloy. This is considered an excellent metal for high temperature applications, with its extreme temperature tolerance used predominantly for aerospace. It’s also a great choice for commercial bellows that work up to 1,600 degrees Fahrenheit. Alongside temperature you should also be considering pressure and pressure changes. Forged steel flanges, for example, eare rated for pressures up to 285 psig at 100 degrees Fahrenheit.
The bellow forming machine has a lot to take into account. It not only needs to be applying the same amount of pressure with each rotation, it also needs to hold strong through temperature changes. Multi-ply bellows consist of two to three tubes, though some models have as many as five depending on the function. Your custom bellows design requires significant focus on no less than 12 vital attributes. These include (but are not limited to) stress modes, flexing, geometric constraints, pressure differential, and vibration.
Bellows are seeing significant improvement as of late. You can thank the surge in applicants for these figures — by the time July of 2017 came around the U.S. Bureau Of Labor Statistics reported as many as 180,000 people working in the oil and gas industries. The United States on the whole has a total solar power capacity of 47 gigawatts. That’s enough to power nine million homes, according to the Solar Energy industries Association. The steps for metal bellows manufacturing is an enduring process and one that only expects to get better.
Today your average bellows are composed of a few tubes. Nickel alloys, stainless steel, and the increasingly popular Hastelloy X alloy are the preferred materials used in their construction. Back in 2015 researchers at Brown University found a new material had the highest melting point of any substance at 7,450 degrees Fahrenheit. A mixture of hafnium, nitrogen and carbon brought about this result and could very well change your industry from the inside out. Just like your pipe expansion joints and exhaust flex pipes need to stay flexible, so too do you need to be receptive to new information.
Keep quality close. Ask yourself, “What can bellows be made of?” and see where it takes you.