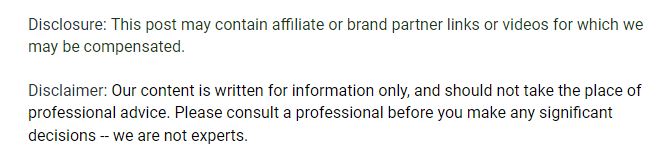

Manufacturing techniques are constantly changing. What is preferred and recommended one day can quickly become outdated and avoided another. Perhaps one of the most commonly changed techniques occurs in the manufacturing of plastic bottles. Although plastic bottles are highly recyclable, they are not always recycled. Because of this, there are constant changes in the manufacturing processes.
The manufacturing of plastic bottles
Plastic remains one of the most produced items on the manufacturing line. Roughly 107.5 billion pounds of plastics and resins were manufactured in 2013, an increase over the previous year?s 105.9 billion pounds. More and more products are specifically designed for plastics manufacturing, most likely due to the fact that it can easily be recycled. Making plastic bottles is likely to continue being one of the most important manufacturing purposes.
The recyclability of making plastic bottles
The majority of plastic bottles that you come across can be recycled. More and more manufacturing plants are taking special steps to ensure high recyclability factors. Although plastic recycling is not at 100%, its numbers are actually high. According to the National Association for PET Container Resources (NAPCOR), 5,764 million pounds of PET bottles and jars were available for recycling in 2013. About 85% of those bottles are used for food and beverages, or 4,899 million pounds. Many states are enforcing higher recyclability rates by charging a minimal deposit. The deposit, usually between 2 and 10 cents is paid upon the recycling of the plastic product. This successful method has resulted in more recycling and the increase in making plastic bottles.
Varying plastic designs
If you think about all the different plastic products in your home right now, you will likely identify many different plastic designs. As of today, the manufacturing companies could choose between the extrusion blow molding, injection blow molding, and stretch blow molding as three methods of this specific industrial process. Although these are the three most common types of blow mold designs, you are likely to find even more variation among blow molded containers and how they are produced. You will also notice a difference between liquid and food plastic containers.
Plastic production for increased marketability
Another cause for differences in plastic manufacturing is for marketability purposes. When you choose your items at the local grocery chain, you look for recognition and plastic packaging that catches your attention. Additionally, your recognition may be influenced by the design or shape of the plastics. Colored bottles, for example, are often used for easy identification of drink items. You can probably specifically remember the color of the drinks that you purchase most often. Bottle companies continue to use these differences in plastic packaging to push brand recognition and to gain customer attention for newer products.
Easier plastics
Plastic manufacturing is also changed by convenience. As the production of plastics improves, so does the ease of the containers. You have probably found that your favorite products are easier to open than ever. Commercial jars of products were once very difficult to open without excessive force. Today, packaging contains easy open caps and easy twist jars. Making plastic bottles requires an attention grabbing package and something that is convenient to customers.
The plastics industry is extremely prevalent in the world. The majority of products that you purchase likely come in some type of a plastic package. Although the plastics packaging industry is constantly changing, it is always changing for improvement and convenience. Making plastic bottles requires careful consideration into marketing, recyclability, and usefulness.