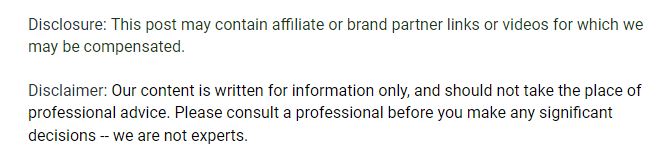

Copper thefts are on the rise. There were approximately 13,000 reported incidents where copper was stolen between 2006 and 2008. That number nearly tripled to more than 32,000 between 2010 and 2012. The increase in copper theft is attributed to its price. Copper is currently valued at over $3 per pound. Globally, copper thefts exceed $1 billion every year. All printed circuit boards (PCBs) use copper. This is the reason the weight of the copper that is used in the prototype PCB manufacturing process.
One of the most important parts of PCB fabrication is the copper. The original metal that was used for the wiring in electronics was brass. It was replaced by copper by the 1950s because it was cheap, easy to work with and is better at conducting electricity. Before the advent of the prototype PCB manufacturing process, the idea of mass production and appeal of the electronic machines and appliances seemed like a very far fetched idea. Electronic products looked interesting but they were bulky and hard to manufacture. The wiring was bulky.
Copper was one of the first metals to be used by humans. Before electronics, it was used for coins and jewelry. Once electronics were invented and its ability to conduct electricity was discovered, copper became a very popular commodity. Today, the main uses for the metal are in electronics and motors. This is the reason its price has risen and people are so eager to steal it.
The reason copper is so good at conducting an electrical current is the ease with which its electrons move within it. The electrons that move through the metal are called “free electrons.” They are also referred to as “conduction electrons” because of their ability to move an electrical charge. These qualities of copper make most of the devices that we love and take for granted possible.
A very important part of the prototype PCB manufacturing and design process is the weight of the copper that is used on the circuit board. When ordering a PCB, it is crucial that the copper weight be specified.
If it is not specified, the default that will be placed on the PCB is 1.2 ounces of the metal. Most often companies need the PCBs with a weight of one ounce or more of copper thickness. The holes of the default PCB have one thousandth of an inch of copper. During the prototype PCB manufacturing process, the boards are plated with half an ounce of copper and then .7 ounces is added for a combined weight of 1.2 ounces of metal.
The amount of current that any PCB can handle is determined by the amount of copper that is plated on it. That is the reason that the copper weight is such an important part of the prototype PCB manufacturing process. The thickness and the weight are also factors that determine the RF circuitry and speed.
When the prototype PCB manufacturing process is started, a dielectric material with copper is applied to both side of the circuit board. Often, the base copper is spread out over a space that is equal to one square foot. The laminates are most often produced with weights that range from half an ounce to three ounces for each square foot. A fabricator will take over the plating. This equipment adds copper until the desired weight has been reached. If a PCB is meant to contain 5 ounces of copper when it is completed, it will start out with a laminate that has three ounces of copper. The fabricator will then add copper until it reaches the specifications of five ounces of copper.
It should be noted that in the PCB manufacturing process is tedious and long and does add to the final price of the PCB. When designing prototype PCBs, it is important to take this into consideration. The need for speed and a higher conductivity must be weighed against the price of the added copper and the costs associated with plating the circuit boards.
Electronic appliances and devices have come a long way and both the advent of the PCB and the use of copper are a big reason these products can be mass produced and enjoyed by so many.