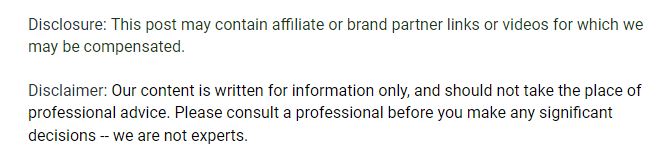
A metal bellows at a workplace such as a furnace or in vehicle engine should not be confused with the air-blowing bellows use in furnaces and old blacksmith shops. Rather, an exhaust bellows or other metal bellows is a tough but flexible tube of metal designed to contain gas or liquid, and these contents are often either extremely hot, extremely cold, or are under very high pressure or may even be corrosive. No ordinary tube or metal can be used to make an exhaust flex joint or a high pressure expansion joint; rather, a high pressure expansion joint can be added to a metal bellows system only if its composition and quality of construction are up for the job. A high pressure expansion joint may be made of different alloys based on the contents that it will carry, and at any workplace, a high pressure expansion joint or other bellows should be regularly looked over to find defects or other developing problems which can be fixed right away. A ruptured metal bellows could cause a major problem if hot or corrosive material leaks out.
What are Bellows Used For?
Metal bellows can be used to safety contain moving liquids or gases, and they may be found in industrial furnaces, chemical plants, vehicle engines, and beyond. They must be flexible but tough to carry materials such as corrosive liquid, extremely hot air, or dangerous gases, and to get this work done, a high pressure expansion joint or other metal bellows will be made of several parts that work to maintain several different aspects of the bellows. Some of these categories include temperature extremes, exposure, vibration, stress, modes, life cycles, and more. The exact composition of a bellows may vary based on what it is carrying, and no matter what, all components of a bellows should be designed specifically for the job, and maintenance is needed to keep them in working order. Hot exhaust fumes in an engine, for example, may be carried by metal bellows further along into the exhaust system until the fumes are released through a tail pipe. Or a bellows may contain something as extreme as molten metal or liquid nitrogen, or powerful chemicals that would dissolve most other materials.
Bellows Construction
If noxious gases, molten metal, or pressurized air are being produced by an engine or factory, no ordinary material can be used to contain them, as mentioned above. Rather, only a metal bellows can get the job done, and even then, using a bellows made from the wrong materials may end in disaster. Just how can the right bellows be used?
The right alloys are usually the answer. Ordinary steel is powerful and useful in many industries ranging from surgical tool to automobiles, but it is not the solution for everything, and certainly not for metal bellows. Rather, specialized alloys are always being developed so that components made from them can endure extremes of temperature, pressure, or chemical composition. Various alloys are designed with certain metals in certain percentages to make for unique properties, and this is useful in many industries. Underwater pipes, for one, are made from alloys that can resist the sea water’s salinity where other metals would corrode, and the same is true of metals and containers found in chemical plants. Extremely hot materials might melt steel or other metals, but an alloy designed to endure it can be used to create a high pressure expansion joint or other metal bellows for the job. To name just one, Hastelloy X alloy is great for high temperature work. This alloy is often used for aerospace but can also be found in commercial metal bellows working with materials up to 1,600 degrees Fahrenheit. Other alloys may endure extreme cold such as liquid nitrogen, or extremes of pressure or chemicals.
Of course, even metal bellows are not indestructible, and they should be routinely inspected for any developing problems such as cracks, loose screws or bolts, or early signs of corrosion. Damage should be noted and reported right away so that repairs or replacement work can be done, and prevent disaster. This can prevent a lot of expensive damage from being done later from leaking gases or molten metals.