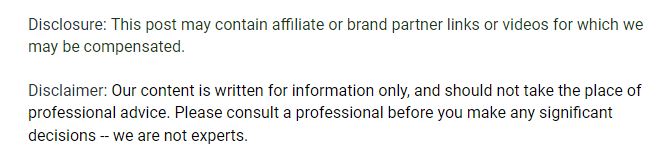
Prefabricated and modular construction processes are used for a variety of building projects. This is not surprising when considering the fact that these constructions can be permanent and relocatable. In some instances, these processes may be used to create an entire project, while in others they are used for a specific aspect of a project.
Types of Popular Modular Construction Projects
A recent survey showed that architects, contractors, and engineers have used these processes on some of their projects. In terms of percentages, this applied to 76% of the participating architects, 84% of the participating contractors, and 90% of the participating engineers.
The commercial construction projects that were completed in 2011, for example, used prefabricated and modular methods for specific application purposes. The survey indicated that these included the following types of commercial projects:
- Healthcare facilities: 49%
- Dormitories and other types of college buildings: 42%
- Manufacturing facilities: 42%
Save Time and Reduce Costs With Modular Construction Methods
It’s important to note that a large percentage of these buildings are constructed within a warehouse or factory. This applies to 60% to 90% of the buildings constructed utilizing prefabricated methods. Given that warehouses and factories are a controlled environment and can be set up specifically for construction purposes, prefabricated and modular building projects can be completed faster than their traditional on-site counterparts.
While it has already been established that this is a faster method of construction, it’s important to note that high quality continues to be maintained. In less than three weeks, or only 19 days, A Chinese modular construction company built a 57-story building.
The Building Industry Association of Philadelphia reported that construction costs can also be reduced when opting for prefabricated and modular building methods. This association has estimated that when project managers and other relevant personnel choose to “go-modular,” that construction costs can be reduced by as much as 9% to 20%.
Energy consumption is also reduced during the modular building process. Recent data shows that this amounts to roughly 67% when compared with traditional building methods. Furthermore, since these buildings are also constructed with energy efficiency in mind, the future occupants will experience a reduction in their overall energy costs as well. These energy savings can be even further reduced when energy-efficient appliances are installed and the occupants engage in additional energy-saving measures.
The waste associated with traditional building methods is also reduced with modular construction projects. As reported by the UK-based Waste and Resources Action Programme, the need for and waste of materials such as the following can be reduced by as much as 90%:
- Bricks>/li>
- Cardboard
- Cement
- Concrete
- Plasterboard
- Shrink wrap
- Wood pallets
Consider How Modular Construction Methods Can Benefit Your Company
You may be interested in the results of the FMI’s 2013 Prefabrication and Modularization in Construction Survey. Nearly half, or 40% of the participating contractors, indicated that having the capacity to engage in prefabrication and modular construction was an integral aspect of their company’s strategic initiative. This does point to the growing awareness of the benefits of these methods for various building projects.
If you have a large warehouse space, for example, one of the more effective ways to create designated workspaces is by installing warehouse partitioning systems such as prefabricated office walls. Just one of the benefits of using prefabricated office walls and partitions is that you can alter office and workspace layouts. Portable office walls are also a convenient option when you and your employees engage in different types of activities that may require altering workspace configurations. Furthermore, when you need to adapt these work areas on a regular basis, portable prefabricated office walls can be easily moved and rearranged so that everyone has the best possible space to perform their jobs.
Does your business need multiple prefabricated office spaces, prefabricated office walls, or other prefabricated construction projects completed? Once you contact a representative to learn more about your options, you will be able to benefit from their expertise. Given their experience, your representative will also be able to provide you with recommendations on how to best configure your site. In the event that you’re in the process of expanding your business, choosing prefabricated and modular building spaces and modifications can save you time and expense.