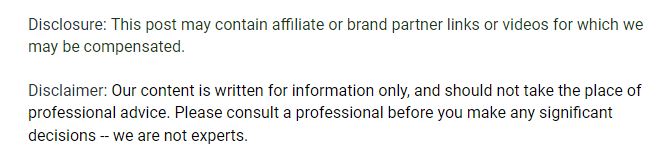

We have come quite a long way since the invention of the wheel. Human beings are capable of so much, and we see evidence of this every where we turn.
Across the pages of every book, in the towering buildings that touch the sky, in the machines that transport us across town, across the country, or to the other side of the world. The evidence is in the lack of deadly diseases that plague us and the quick recovery times of those who develop sicknesses that used to wipe out entire populations. It is seen in the connection between two businesses or individuals separated by thousands of miles and brought together by the touch of buttons and pictures on screens.
The developed world is certainly something to be marveled at, in every respect, right down to the tool engineering that makes so much of these industries possible.
Tool engineering that builds the basics of society
By this point in the evolution of our societies, there are countless branches of systems that make everything work together as it should. Countless building blocks and endless aspects of foundations factor in to creating a society that functions on every level, from infrastructure, businesses, education, economics, environment, and so much more. And if you strip down to the basics of the machine industry that contributes so much, you will find that tool engineering allows so many aspects to work together seamlessly. The tooling manufacturing industry has a market size right around $90 billion, making it one of the most important aspects and a key industry in the sector of manufacturing as a whole.
Cutting tool engineering in the manufacturing business
As various as there are uses and needs for machines, so there are just as numerous tools and processes for manufacturing. In general, those who make these machine tools, gauges, dies, fixtures, molds, jigs and other elements for manufacturing purposes are referred to as tool and die makers. Dies are the tools that manufacturers use to shape or cut materials, and there are several different types, as one might imagine, considering all of the different items that are made with them. Cutting tool technology, like most types of technology that has been existent for more than a few years, has evolved and developed over the years.
Different types of cutting tools
Carbon tool steels were some of the first used for cutting with their good machinability, but loses hardness around 250 degrees Celsius, so cannot be used in applications with excessively high temperatures. Around 1900 is when high speed steels, or HSS, were developed, and could cut about four times faster than carbon steels. The class of high speed steels is itself complex, with more than 30 different grades separated into the three categories of tungsten, molybdenum, and molybdenum cobalt based grades. Cemented carbide tools can stand up to extremely high speeds and temperatures up to 1000 degrees Celsius, but ceramic tools can make it all the way up to 1800 degrees Celsius, greatly overshadowing the other types.
Our societies will continue to grow. Industry will continue to develop, tying in more closely with modern technology and the digital age. As long as we can successfully shift attention and awareness to how carelessly our industrial advancements of the past were handled, we can continue to move forward in all aspects of development, better caring for the planet as we go. If that shift does not occur, the potential for development and advancements we haven’t even begun to think of yet will still be there. But our resources, our species, or this planet that is our home might not. We have a responsibility and a duty of care for the earth that our industrial advancements have not always aligned with.