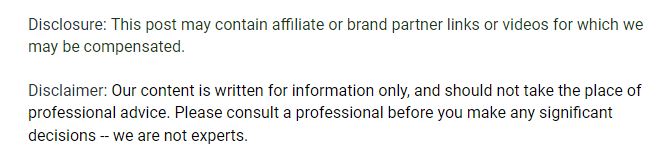
In today’s world of industry, working with metals is essential for the construction of nearly anything from cars and trucks to tractors, electrical appliances, and much more. Metals occur naturally in the earth, such as iron, nickel, and copper, but today’s manufacturing demands high quality alloys and other metals such as steel. Different alloys are used for various conditions that normal metals cannot endure, such as extreme heat or cold, salty water, high pressure, corrosive acids or gases, stress, and more. Often, an alloy will be tailor made for an environment such as inside a train engine or a pipe running through miles of salty ocean water, and there are recipes, to put it one way, of alloys based on how they are intended to be used. These alloys and other metals come from an induction furnace, where all kinds of industrial work can happen, such as induction hardening, steel melting, and more for building machine spare parts and much more. Replacement parts for these furnaces and other facilities may be needed every so often as the components in an induction furnace break down. What do induction furnaces provide for today’s industry and metal needs?
The Market For Metal
Metal is found nearly everywhere, and the world, especially the United States, is always eager to manufacture or import it. Crude steel production, for example, reached 1.69 billion tons around the world in the year 2017, and this represents a 3.9% increase from 2016’s production. Up to half of the world’s supply of steel goes toward infrastructure and buildings, although it can be used for much finer wares such as surgical knives or kitchen utensils (often stainless in both cases). Another 13% of the world’s steel is consumed in the automotive industry, another massive industry, and 16% of global steel is dedicated to mechanical equipment, like manufacturing or robotics.
The United States and Canada often import steel for their hungry industries, with the United States being the world’s biggest steel importer. $27 billion worth of steel was imported in 2017, and in 2016, Oxford Economics showed that 88% of steel exported by Canada was brought into the United States, which makes up 17% of the total steel that the United States imports. As for what to do with all this raw steel, an induction furnace is often useful this metal and others to create alloys for all kinds of industries.
Inside an Induction Furnace
According to Atlas Foundry, induction melting happens when a primary coil sends a high voltage electric source to a low voltage, high current metal secondary coil, and this constitutes a transfer of heat. An induction furnace is ideal for melting and alloying metals, although not for refining them. One such type is a channel furnace.
A channel induction furnace is a refractory lined steel shell that holds molten metal inside. An induction unit acts as the melting component of the furnace and is connected to the shell by a throat. This induction unit is made up of an iron core ring that has a primary induction coil wrapped around it. All together, this forms a transformer that molten metal loops in, and heat generated in the loop will cause the metal to circulate into the furnace’s main well. This also causes a useful stirring action during the melt, making the whole process smoother.