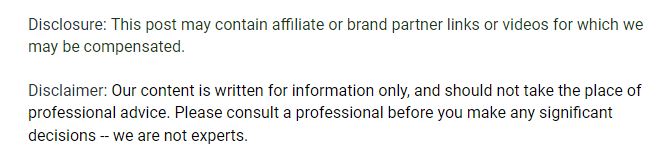
Ceramics is a term to describe materials made from non-organic compounds and ingredients such as metals and non metals, and they are often valued for their heat-resistant nature, making them ideal for baking in a kiln or using in other items that produce extreme heat, as they will not easily melt or get discolored due to flames and intense heat inside. Ceramic materials, then, are often used by and made inside furnaces, kilns, and other very hot items, but sometimes, ceramics may need extra protection to increase their longevity and their resistance to heat. Some brands such as ITC 100 can help with this, and ITC 100 application onto ceramic surfaces can result in ceramic insulation that is more effective and long-lasting than ever before. The best ceramic coating may be found when a customer, whether a private owner or a business professional, contacts experts and asks them for guidance on application of ITC 100, or to hire crews to apply ceramic coating kits into ceramic surfaces for industrial use. With all this in mind, how can one find and apply the right cement coating or ceramic insulation coating, and what are some general trends in heat-based work?
Kilns and Furnaces
Sometimes, work can only be done when a lot of heat is applied to materials. In fact, the average kiln will heat up to temperatures ranging from 1,800 to 2,400 degrees Fahrenheit, and the earliest known kilns can be traced back to 6,000 BCE. These kilns could be fired up to 900 degrees Celsius, or 1,652 degrees Fahrenheit. When using a kiln, a person is urged not to place items inside to within one and a half inches of the kiln’s elements, and a typical kiln’s elements will last for about 100 firings before needing to be replaced. Just why is so much heat needed? After all, ceramic is very heat resistant and can endure temperatures up to 3,800 degrees Fahrenheit, or 2,000 degrees Celsius, and these temperatures are needed to work with raw ceramics that are placed inside. And what is more, temperatures of up to 5,000 degrees Fahrenheit are possible in a kiln whose ceramic surfaces have been coated with ITC 100.
For these reasons and more, a private owner of a kiln or a commercial owner of many kilns or furnaces is encouraged to make sure that their heat- dispensing items are capable of enduring very high temperatures for work, and this can help prevent disaster, such as the machine damaging itself from the heat or ruining the item inside. Not only should the kiln’s heating elements be replaced when they are worn out, but ceramic surfaces inside can be coated with protective materials so that they can endure higher temperatures and resist damage over time. A company that works with kilns can purchase ITC 100 and other coating products and have a qualified professional apply this material to the ceramics, and once the coating is done and dry, the kiln will be ready for work, more efficient than ever. Private kiln owners can search online or at local hardware stores for ITC 100 and similar products, and either apply it themselves or hire a professional to take care of this work. If a good job has been done, then a kiln’s ceramic features will be ready for next level work. This may be an essential component of kiln repair, since from time to time these machines may wear out with age and their ceramics may get damaged or worn out, or heat may leak from one part of the machine to another and damage it.
Someone who buys a used kiln must have it inspected and repaired as needed before use, as a faulty kiln may very well damage itself with heat once it is fired up. Parts inside the kiln can be repaired or replaced as the inspector suggests, and this may often involve replacing the ceramic heating elements and applying ITC and other protection onto the surfaces so that a used kiln can operate with maximum temperatures and safety for years to come. This helps ensure that a used kiln is a good investment and lasts a long time.