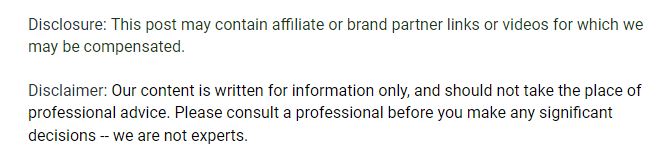
Manufacturing in the United States is enormous, and a variety of materials are used to construct everything from buildings to cars to kids’ toys and computer parts. Among these are thermosetting polymers such as polyurethane and related materials, which are recent but highly effective materials. Older materials such as bricks, metal, glass, and rubber have their uses as well, but reaction injection molding is best done with polymers that are best designed to cure quickly in their molding process. Structural foam molding is also possible, along with using injection molded enclosures and Polyurethane injection molding is another fine option, and many factories in the United States and the rest of the developed world constantly produce both these polymers and their goods. And on top of that, the uses of polymers don’t end with reaction injection molding. Plastic is easily recycled, and anything made out of reaction injection molding may be later repurposed. This can help protect the environment.
Basics of Reaction Injection Molding
This describes the process that creates molded polyurethane parts, such as car fenders and air spoilers. This process involves combining two liquid components when injection is done in the mold, and as reaction injection molding takes place, the two components chemically react and cure. These components will permanently intermingle and start curing into a solid, cool material inside the mold, being a thermosetting type of material. This material is also distinctive for being made up of microcellular systems, meaning that they contain cells as small as 0.001 inches in diameter each. In some ways, they may even resemble a living thing in this manner. The wall thickness for these polyurethane goods doesn’t have to be very thick to do its job; in fact, the wall thickness for reaction injection molding goods is typically 1/8 inch. In other cases, when need be, a reaction injection molding product may have wall thickness as great as half of an inch. Whether thick or thin, these walls are part of a product created in great pressure; the reaction injection molding machine applies pressure ranging from 1,500 to 3,000 psi to blend the two plastics (by means of impingement) to ensure a good blend. This results in a product that is light but tough and durable, useful in many different arenas. But what about after a product’s viable life? What happens then?