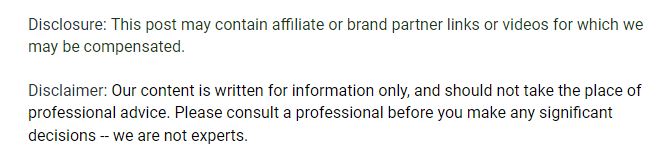

Planning pays off, and when it comes to planning a safe work environment it is essential that your plans are both detailed and up to regulation. In an attempt to make work sites as safe as possible, the Occupational Safety and Health Administration (OSHA) has specific requirements for wire rope slings, rigging supplies, and all other kinds of fall protection equipment. Understanding both the installation and the maintenance of rigging supplies and other protective measures, however, is not enough. Workers must be periodically trained and tested in their knowledge of how these important pieces of equipment are used.
The guidelines are extensive and are updated as new research and new materials become available, but the attention to detail helps protect workers, employers, and valuable expensive equipment and materials:
- Sling types can be endless, single, two, three, or four leg.
- The measurements for wire ropes are expressed in number of strands times the number of wires. For instance, a 6 x 25 rope has six strands and 25 individual wires.
- All fall arrest systems must be tested with a weight of 300 pounds, plus or minus five pounds, according to OSHA.
- Yearly, monthly, or other periodic tests are required for all fall arrest devices. It is important to check with the latest OSHA guidelines to know that you are up to date on all of these requirements.
- Simple summaries can help workers remember the basic procedures that are needed in many types of precautions. For instance, OSHA uses a three step process to prevent dangerous falls and save lives. The steps plan, provide, and train are easy to remember and can be posted throughout a work site.
- An important safety issue is to remember the specific safety standards for individuals of different heights and for items of different weights. For example, OSHA requires that general industry workplace fall protection be provided at elevations of four feet; five feet in shipyards; six feet in the construction industry; and eight feet in longshoring operations. As far as individual safety standards go, workers who are at six feet or more above lower levels are at risk for serious injury or death if they should fall. To protect these workers who are at taller heights, employers must provide fall protection and the right equipment for the job, including the right kinds of safety gear, ladders, and scaffolds.
- Fewer injuries mean a more positive work place and more profits to both the company and the employees. As such, many companies offer incentives to teams or departments that produce zero injury statistics for extended periods of time.
- Everyone needs to be knowledgable about rigging supplies and other fall protection equipment and procedures.