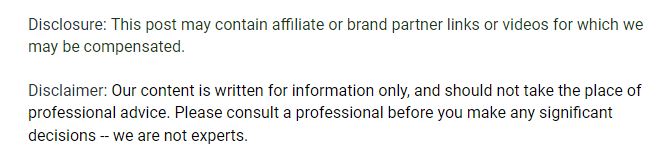
The world of construction is confusing and complex to anyone on the outside looking in. This is mostly because of the range of machines and tools used to build construction projects. This includes a surge machine, vibratory screeners, and a screen. Here are some random facts about construction projects and the screen.
The most popular barrel dimensions for tumbling drums will vary in diameter, anywhere between 18-inches and 36-inches and in length 18-inches and 42-inches. For the most part, the diameter is usually smaller than the length so that the tumbling drums can be proportional. Horizontal barrel speeds vary from 20 to 38 RPM, depending on the barrel size and the items to be tumbled.
Depending upon the amount of material to be removed from the parts, tumbling will take anywhere from 6 to 24 hours. For dry tumbling, the horizontal octagonal barrel is used almost exclusively. This barrel sometimes has a metal skin and a hardwood lining which can be replaced when necessary. A barrel that is 30″ in diameter by either 36-inches or 42-inches in length is considered standard.
Barrel speeds in dry tumbling are generally kept at 28 to 32 RPM. If given time and careful handling, plastic parts can be polished to a finish that approaches hand buffing. Since the media is comparatively light, it takes a 10 to 15-hour run to get results. The number of parts which will fit safely into a barrel will be determined by the barrel size, size of the part, the part’s fragility, shape and weight and the end result desired. Parts usually account for one-third of the total barrel load.
Barrel load heights, including the parts and media, should not be less than 45% or more than 60% of capacity. Load heights between 40% and 45% produce more action but a poorer finish. This is the best way to protect a screen from damage on the construction site. Barrel loads can be heavy and it is important to keep items like the screen safe.
For barrel loads, the optimum load height is 50%, with approximately three parts media to one of parts to keep parts from impinging. Rotary crushers are typically built with shaft impactors to create considerable force. Ideal for both recycling and food processing, they can be calibrated for a size reduction ratio between 10:1 and 25:1. Rotary speed varies from 85 rpm to 1,200 rpm. Modern models can be customized with different sets of hammers that enable the machine to work on different materials.
Screening falls into two general categories: dry screening and wet screening. From these categories, screening separates a flow of material into grades, these grades are then either further processed to an intermediary product or a finished product.
High-frequency vibrating equipment is a shaker whose frame is fixed and the drive vibrates only the screen cloth. High-frequency vibration equipment is for particles that are in this particle size range of an eighth in down to a mesh. Two-compartment barrel mill is designed for dry milling of construction materials of low and medium hardness.
Anyone that works in the field of construction shouldh ave some idea on how to properly utilize a screen. This will help them handle intense vibrations as well as large loads.