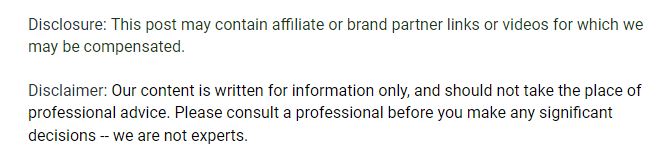
Many tools and measuring devices are used in industry today, from factories to car repair shops and beyond, and these tools should be in good shape. Measurement tools like load cells, for example, use various methods such as fluid pressure or warped metal rods to measure how much weight, or resistance, they are experiencing, and these pressures form electrical currents that in turn lead to a readout that someone can see. Meanwhile, torque is very useful for certain wrench types, and torque can allow a worker to secure a nut or bolt or other item, such as on a car wheel. But if the strain is too great, a torque tool may do more harm than good during a day’s work, so measurement tools like calibration wrenches must be used to get everything back into working order. Force measurement is the common thread between these two device types. How can these measurement tools do good?
Load Cells and Their Types
For many industrial items, big and small, it is important to know exactly how much an item weighs, and the “scales” used by factory workers, construction workers, and other professionals is various load cell types. The basic idea of these measurement tools is for an item to be placed on their platform, and that pressure, or resistance, warps a fluid or metal in the load cell and in turn creates an electric current, as described above. This current feeds data into the load cell’s computer which then creates a useful reading, such as pounds, grams, kilograms, or even tons. In fact, based on their type, loading cells can achieve accuracy around 0.03% to 1%, depending on the particular type, and if they are properly installed and calibrated by professionals, they will continue giving off highly accurate readings. These devices are non-intrusive, which adds to their appeal since they don’t actually interact with the weighed item aside from placing that item on a loading cell’s platform.
Different models of load cells exist, and they differ on their measurement method and exact specifications. These measurement tools may, for example, be the strain gauge model, which is one of the most common types. Strain gauge load cells are well established in industry today and have proven their merits for over 40 years. Meanwhile, hydraulic load cells make use of liquids and pressure to measure resistance, and these load cell types can operate at temperatures as low as -60 degrees Celsius, or -76 degrees Fahrenheit, which may make them useful in frigid environments such as at a work site in the Arctic Circle. Diaphragm load cells, spool type load cells, and ring type load cells are also all on the market for work sites that need them, such as car garages or repair shops.
Torque Wrenches
Ever since their invention by Conrad Bahr back in 1918, these tools are essential to modern construction and repair work, such as at a car garage or a factory, and they will often have measurement tools attached to them that give accurate readings of how much torque, or rotational power, is being applied to an item by means of that wrench. The issue here is that with too little torque, the work is not done, and with too much, the strain might damage something. Normally, measurement tools on these wrenches should be accurate, but sometimes those gauges will lose their accuracy over time. If a worker suspects an accuracy issue, he or she may fix this problem with a calibration wrench.
A calibration wrench is a torque wrench that, instead of being used for everyday work, is only used as a comparison, and a control group, with afflicted torque wrenches. Such wrenches are always accurate and thus function as the control group, or the standard. The worker can start calibration by using the calibration wrench on an item, then do the same job with the faulty wrench and see the difference in the readouts. The worker can adjust the faulty wrench’s measurement sensors, and repeat this process a few times, getting the faulty wrench’s readings more accurate until they finally match that of the calibration wrench.