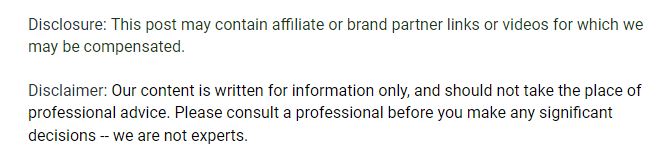
It’s one thing to store water. It’s another to store milk. When storing chemicals that run the gamut from sensitive to dangerous, only a very specific kind of method will do.
This is the underlying logic of stainless steel chemical tanks and all the unique varieties they come in. When fulfilling the part of the pressure vessel manufacturer you need to ensure everyone is on the same page. This means explaining the function of the tank cooling jacket and going over the basics that set stainless steel apart from other metals. Chemical storage tanks have the unique issue of potentially losing quality when insufficient and putting others in danger. Preventing leaks, cracks, and dropped temperatures starts with a single question.
How do stainless steel chemical tanks work?
How Is Stainless Steel Determined?
The most important part of respecting stainless steel’s potential is knowing how it’s made. Stainless steel is a generic term used to denote multiple types of steel that have a bare minimum of 10% chromium by mass. It’s called ‘stainless’ due to its inability to rust (except under rare circumstances, such as an insufficient amount of chromium). Alongside stainless steel you have carbon steel, aluminum, and copper sitting at the top of the list of most used metals in the world. Chemical holding tanks especially benefit from this sturdy material.
What Does Stainless Steel Transport?
Did you know steel has been used to both store and transport water for over 150 years? It’s durable enough to hold up to nearly any type of weather and flexible enough to still be recycled and repurposed. Stainless steel chemical tanks are relied upon to ensure the liquids inside retain a consistent temperature without exposing workers to leaks. The United States remains the top steel-producing industry in the world, employing over 140,000 people. The staying power of steel can easily be traced to its durability.
Just How Strong Is Stainless Steel?
When asked which material holds up the best to pressure, temperature, and time itself, stainless steel crops up again and again. Carbon steel, for starters, has a tensile strength of over 550 megapascals (or Mpa), with a yield strength of over 250 Mpa. You can find stainless steel layered over a faucet handle as well as constituting the dominant material of shipping containers. The latter is so widespread, in fact, they’ve started to be used outside of their original purpose. Stainless steel shipping container restaurants and offices are becoming an increasingly common sight.
What Is Dimple Jacket Heat Transfer?
Stainless steel chemical tanks need to be outfitted with certain accessories to ensure they never lose a certain temperature. Dimple jacket heat transfer, or dimpled stainless steel, combines both the natural power of steel with a unique design. Several rows of strategic dents are applied throughout the sheet, then layered within chemical holding tanks to help them manage heating and cooling processes. These can be removed and replaced easily, adding some much-needed flexibility to a busy industry. With the proper amount of chromium these will also be resistant to rust.
How Can Chemicals Be Better Protected?
The cooling jacket for reactor is a necessity to keep chemicals protected at all time. Your first order of business is to ensure you’re applying the correct amount of ingredients into each tank cooling jacket you create. A lack of chromium can cause metal to rust, then exposing workers to potentially deadly combinations. Steel of an inferior strength can also be more easily dented and wrinkled, creating damage throughout the transportation process. Time and time again, stainless steel teaches us it’s the little things that matter most.
How will you create the most efficient jacketed reactor?