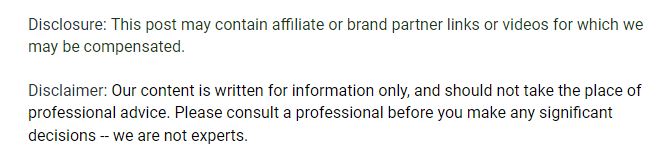
The construction industry is enormous, and many construction contractors are hired to build schools, banks, libraries, apartments, hotels, and office buildings, among others. This is a $1 trillion industry, and naturally, engineers and other innovators are looking for new ways to make this work more efficient than ever. Fortunately, some solutions have been found, such as using prefabricated office spaces, warehouse partitioning systems, and other modular office technology. Not every building or room is made this way, but building and buying prefabricated office spaces has its benefits, such as lower costs and resource efficiency. More and more often, today’s buildings have prefabricated office spaces and modular rooms fitted in, and some hotels or apartments might be built almost entirely with them. How does it work, and how efficient is this kind of construction?
Modular and Prefabricated Rooms
The idea behind prefabricated office spaces and other modular rooms is that a given room is built indoors, separately from the construction zone itself. In the workshop, a modular room will be built from the ground up, including its frame, flooring, windows, and water and electric utilities. It will also be fully fabricated, and by the time it is shipped to the construction zone, all that’s left to do is to fit it into place. Such modular rooms are shipped ready for use, and they can be delivered via heavy trucks. Once at the site, cranes can lift them into place on the structure, and workers will connect the utilities and get the room operational. Once that is done, there is very little left to do, and such rooms have fairly low maintenance needs.
Why do this at all? Modern prefabricated office spaces are less costly to build and install than constructing them at the site, and the workers are safe indoors while making them. While these rooms are built indoors, resource efficiency is high, and many room builders can recycle leftover materials and avoid waste. As a whole, using prefabricated office spaces is a great way to avoid construction waste, and in the modern day and age, resource efficiency is something that many companies take seriously. At a regular construction zone, junk removal services must be hired to cart away all leftover scraps, such as damaged bricks, wood bits, concrete, and more, and this is an extra expense. But buying modular rooms can avoid that issue entirely. The UK-based WRAP (Waste and Resources Action Programme) determined that modular construction methods like these can reduce material waste by as much as 90%. This includes cement, concrete, bricks, timber, wood pallets, shrunk wrap, plasterboard, and cardboard.
Often, offices are built like this for a skyscraper or other place of business, but that is not the only option where modular prefab rooms are concerned. Bathrooms can be built like this too, not to mention break rooms, and many hotels are also using this tech for guest rooms. In particular, Marriott international pledges to use modular construction methods for 13% of their North American developments in the year 2017. And while modular construction methods haven’t totally replaced traditional construction, this is a common route to take. In the year 2011, prefab modular construction was popular for commercial applications such as healthcare facilities (49% of respondents reported using prefab tech this way), dormitories and college buildings (42%), and manufacturing facilities (42%).
It may also be noted that modular buildings can be either permanent or mobile. A construction company manager, for example, will want a mobile office that they can relocate to any current construction project site, and a mobile modular office is just the thing they may need, fully fabricated.
Warehouses
Modern warehouses need enough room to store all items found inside, not to mention shelves, carts, and rooms to keep everything sorted and organized. Warehouses use relatively few fixed walls or doors; instead, warehouse partitions can be set up, taken down, and moved around as needed, and they can be bought pre-fab and ready to use. Many of these walls may include windows and/or doors, and they can be used to form temporary rooms that people can enter and leave at will. Warehouse managers can also use modular, mobile offices in the middle of the warehouse floor, complete with windows and running electricity.